Product
Our goal is to minimise the environmental impacts of our products during their manufacture, installation and in use. Our products today are inherently sustainable, providing long-lasting durability and performance with no, or minimal maintenance requirements and are typically recyclable at the end of their life. However, there is even more that we can do.
THE CLAY BRICK: TIMELESS BEAUTY, UNRIVALLED DURABILITY
The clay brick has been used as a building material for centuries. Through improved manufacturing technologies and efficiencies, the modern brick of today is more durable and significantly less energy intensive than its predecessors, whilst also maintaining its aesthetic appeal and reputation as the nation’s building material of choice. Produced to exacting standards, the lifespan of buildings constructed from clay brick is typically greater than 100 years, literally spanning generations. There are countless notable examples of celebrated architecture in the UK’s built environment which demonstrate the longevity, and beauty of this most simple of materials. Many homes built in the Victorian period were built from brick and are now sought after due to their spacious interiors, robust construction and typically large gardens. To many, the beauty of these buildings has increased with age, defined by the character of the clay bricks which have gently weathered over the last century. On a wider scale, a 2017 survey1 by BRE Trust revealed over 20% of the UK’s housing stock built from clay brick is over 100 years old. Many of these homes will have been adapted and extended since their initial construction, but that underlying trust in brick as the core material in these buildings remains

The carbon footprint associated with clay brick manufacture remains significant, primarily through the use of natural gas fired kilns, and the natural chemistry of clay minerals. Over the extensive lifetime of a clay brick-built building, the lifecycle carbon impact is remarkably low. Clay bricks also possess strong thermal mass qualities, helping minimise the impacts of more extreme weather conditions through their strong heat absorption; increasingly important as climate change increases the frequency of these conditions. During winter, bricks store heat on sunny days, slowly releasing this back to help warm the building. During the summer, heat is buffered and the interior of a brick building remains cool on the hottest days.
The longevity of brick is further complemented by the inherent quality of brick structures to require no, or minimal maintenance throughout their long lifespan, whereas many alternative materials may require repeated application of protective coatings / treatments to extend their lives. The nature of a clay brick structure makes adaptation relatively easy; parts of the structure can be removed and modified with relative ease, further enhancing the lifetime of the building. When a clay brick building does reach end of life, usually as a result of conscious demolition rather than condition, the materials can be reclaimed with the bricks themselves being reused if in good condition, or alternatively being crushed to be used as raw material within further construction applications.

PRODUCT INNOVATIONS
Our product innovation, and research and development programmes are centred on two key themes: to meet the adapting needs and requirements of our customers in how they build, and to support the UK’s ambition to transition to a lower carbon economy. Specific focus centres on the increasing requirement for offsite precast, and masonry façade solutions, utilising modern methods of construction to improve site efficiency, reduce wastage and support ambitious national housebuilding targets to provide better standards of homes for all.
Our drive for further product innovation will continue. By 2025, we have set a target of 10% of revenues to be generated from new and sustainable products, focused upon offsite solutions, and the use of alternative raw materials where the positive impact upon our carbon footprint can be clearly demonstrated.

Sustainable sourcing
Local sourcing of raw materials isn’t always possible and where we do need to transport materials longer distances, we seek to do this in the most sustainable way possible. We utilise the rail network to transport pulverised fuel ash (a key raw material which in itself is a waste product used in manufacturing our Thermalite aircrete blocks) to our factory.
Since 2015 we have transported almost 400,000 tonnes of material by rail, removing over 4m heavy goods vehicle miles from the UK road network whilst also reducing carbon emissions.
Plastics packaging Reduction
The reduction of polythene plastic packaging supplied with our products provides a huge opportunity to support the wider global environmental goal in the reduction of single use plastics, and the associated harmful impact upon natural habitats when these materials are not disposed of appropriately.
Our current packaging provides benefits including ease of product identification, stability during transportation, and ensures our products are clean, dry and fit for installation upon construction-sites.
We already minimise plastic packaging on many of our product ranges, including our aggregate blocks and specific brick ranges, and have also significantly increased the recycled content of essential plastic strapping to ensure stability. However, as a business we have generally experienced overall increases in plastic packaging, consistent with the wider trends in society across other everyday products.
Our targets in meeting this challenge are ambitious, with a commitment to reduce our total volume of plastic packaging by at least 50% by 2025, whilst also ensuring that the safety and quality credentials provided by our current packaging methods are not compromised.A dedicated project team is tasked with the delivery of these targets, including capital expenditures for the upgrading of packaging machinery and general innovation in packaging solutions.
To illustrate in context, this targeted saving of 976 tonnes of plastic per annum is the equivalent of 195 million plastic carrier bags.
To ensure consistency in customers’ supply chains, we recognise that this is a topic requiring full industry engagement and collaboration, and we have begun working with customers across
all of our key markets to ensure our solutions meet their needs.
2025 Target
50% reduction in plastic packaging
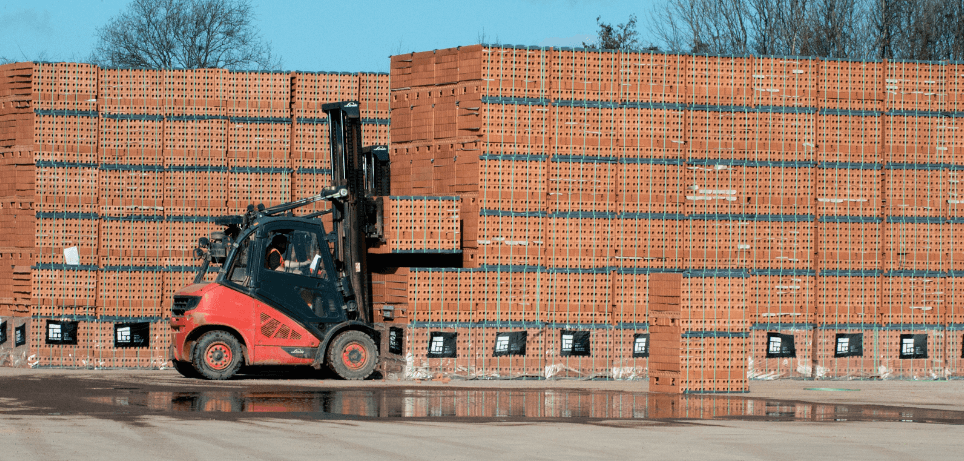